In today’s tech-driven world, the role of a PCB manufacturer is crucial for the electronics industry. These manufacturers create printed circuit boards that serve as the backbone for countless devices, from smartphones to medical equipment. Understanding what a PCB manufacturer does not only sheds light on the production process but also highlights the importance of quality and innovation in technology.
Understanding PCB Manufacturing
PCB manufacturing involves the creation of printed circuit boards, essential components in electronic devices. This process encompasses several steps, each critical for producing high-quality PCBs. Companies like WellPCB offer advanced PCB manufacturing services, ensuring that all production phases, from design to assembly, are carried out with precision and efficiency.
Definition of PCB
A printed circuit board (PCB) serves as a foundation for connecting electronic components. It consists of a non-conductive substrate, such as fiberglass, layered with conductive pathways made of copper. These pathways allow electrical signals to pass between components, facilitating the operation of devices.
Importance of PCBs in Electronics
PCBs play a crucial role in the functionality of electronic devices. They are integral to products like smartphones, computers, and medical equipment. PCBs ensure the reliable operation of circuits by providing a compact and organized layout for connections, reducing the likelihood of faults. By optimizing space and maintaining electrical integrity, PCBs contribute to the efficiency and performance of electronic systems.
Types of PCB Manufacturers
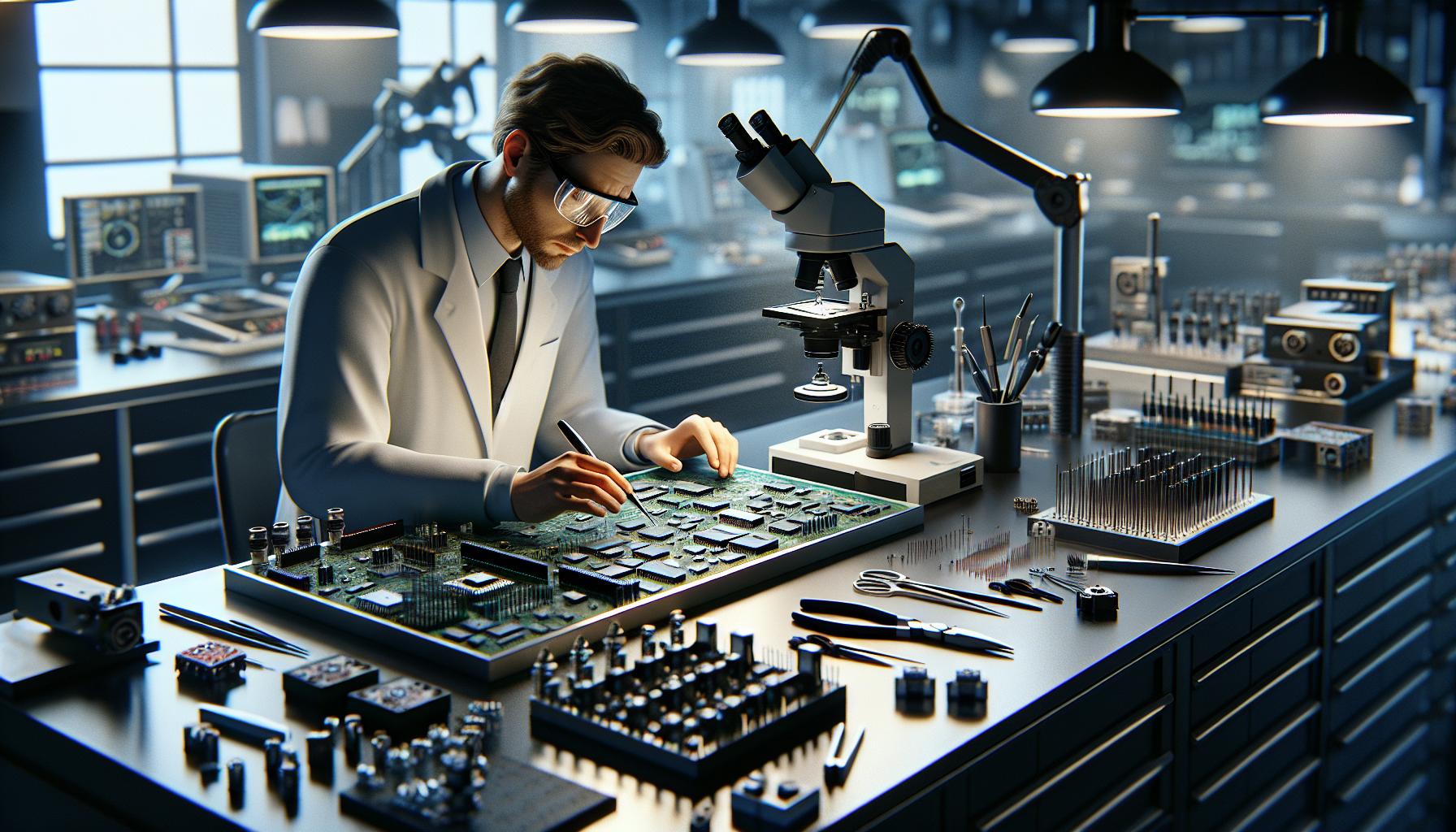
PCB manufacturers can be classified into several categories based on location and specialization. Understanding these types helps in selecting the right manufacturer for specific needs.
Domestic vs. International Manufacturers
Domestic manufacturers operate within a specific country, providing advantages like shorter lead times, easier communication, and adherence to local regulations. They often focus on markets that require quick turnarounds or specialized attention. Examples include firms that support local industries like automotive or aerospace.
International manufacturers, on the other hand, typically offer lower production costs due to economies of scale. They may provide a broader range of capabilities and technologies. However, challenges like extended shipping times and potential language barriers can arise. Choosing between domestic and international manufacturing often depends on project requirements, budget, and quality expectations.
Specialized vs. General Manufacturers
Specialized manufacturers focus on niche markets, producing PCBs that meet specific industry needs, such as medical, automotive, or high-frequency applications. They generally possess advanced technologies and expertise in unique manufacturing processes, ensuring high standards and reliability.
General manufacturers cater to a wide range of sectors, producing standard PCBs for various applications. They often prioritize volume production over specialization. These manufacturers are suitable for businesses needing affordable solutions with less stringent requirements. Selecting between specialized and general manufacturers hinges on the complexity of the project and performance standards required.
Key Processes in PCB Manufacturing
PCB manufacturing involves several key processes that ensure the production of reliable printed circuit boards, integral for electronic devices. Each step plays a crucial role in maintaining quality and functionality.
Designing the PCB
Designing the PCB includes creating a schematic diagram that defines the connection of electrical components. Engineers use software like Altium Designer or Eagle to lay out the board’s circuitry. The design must consider factors such as component placement, signal integrity, and thermal performance. Once finalized, the design undergoes validation through simulation, identifying potential issues before production begins.
Fabrication Techniques
Fabrication techniques translate PCB designs into physical boards. This process typically involves several stages:
- Printing: A photoresist is applied to the substrate. Light exposure transfers the circuit pattern onto the resist.
- Etching: Excess copper is removed, leaving the desired circuit pattern on the board.
- Drilling: Holes for component leads are drilled at specified locations.
- Plating: The drilled holes are plated with copper, ensuring conductivity between layers.
These steps finalize the bare board, ready for further assembly.
Assembly Processes
Assembly processes connect components to the fabricated PCB. Two primary methods dominate:
- Surface Mount Technology (SMT): Components are soldered onto the board’s surface using automated machines. This method optimizes space and increases assembly speed.
- Through-Hole Technology (THT): Components with leads are inserted into pre-drilled holes and soldered. This process creates stronger connections, suitable for larger components.
Post-assembly, the boards undergo testing to ensure functionality and reliability before distribution.
Quality Control in PCB Manufacturing
Quality control plays a crucial role in PCB manufacturing, ensuring that every printed circuit board meets stringent performance requirements and reliability standards. This process involves multiple steps, including adherence to industry regulations and thorough testing methods.
Standards and Certifications
Manufacturers adhere to specific standards and certifications that guarantee quality and reliability. Common standards include IPC-A-600 for PCB acceptability and ISO 9001 for quality management systems. Certifications like UL, CE, and RoHS indicate compliance with safety and environmental regulations. These standards help maintain consistency in production and build trust with customers seeking high-quality printed circuit boards.
Testing Methods
Testing methods confirm the functionality and reliability of PCBs before distribution. Key testing techniques include:
- Automated Optical Inspection (AOI): Utilizes cameras to detect defects on the PCB surface, ensuring the accuracy of component placement and solder joints.
- X-Ray Inspection: Examines internal layers of the PCB, identifying defects not visible externally, particularly in multilayer designs.
- Functional Testing: Simulates the PCB’s intended operation to verify overall functionality and performance under real-world conditions.
- Environmental Testing: Assesses PCB performance under various environmental conditions, such as temperature and humidity, to ensure durability and reliability.
Each testing method plays a vital role in the quality assurance process, minimizing risks associated with PCB failures and enhancing customer satisfaction.
Trends in PCB Manufacturing
The PCB manufacturing landscape constantly evolves, driven by technological advancements and pressing environmental concerns.
Innovations in Technology
Emerging technologies significantly improve PCB manufacturing capabilities. Automation plays a crucial role, improving production speed and reducing human error. Machine learning algorithms optimize design processes, allowing for rapid iteration and reductions in time-to-market. Advanced materials, such as flexible substrates and high-frequency laminates, accommodate the growing demand for lightweight and high-performance PCBs. Additionally, the introduction of 3D printing in PCB prototyping streamlines development, enabling faster product testing and iterations.
Environmental Considerations
PCB manufacturers increasingly focus on sustainability. The shift from traditional manufacturing processes to eco-friendly techniques minimizes waste and energy consumption. Utilizing lead-free solder and recyclable materials aligns with stringent regulations. Strategies such as closed-loop systems and efficient resource management contribute to reducing the environmental footprint. Manufacturers are also investing in initiatives that promote circular economy principles, ensuring that electronic waste is responsibly managed through recycling and reusing materials.
Conclusion
Understanding the role of PCB manufacturers is crucial for anyone involved in electronics. These manufacturers not only produce the essential printed circuit boards that power devices but also ensure quality and innovation through rigorous processes and standards. As technology evolves, so do the manufacturing techniques and materials used, making it vital for businesses to stay informed about industry trends. Selecting the right PCB manufacturer based on specialization and location can significantly impact project success. By prioritizing quality and sustainability, manufacturers contribute to a more efficient and responsible electronics industry.
Frequently Asked Questions
What is a printed circuit board (PCB)?
A printed circuit board (PCB) is a fundamental component in electronics, serving as a base for connecting various electronic parts. It consists of a non-conductive substrate layered with conductive pathways made of copper, allowing for efficient layout and connections, which enhance device performance and reliability.
Why are PCB manufacturers important?
PCB manufacturers are vital to the electronics industry, as they create the printed circuit boards that power devices like smartphones and medical equipment. Their expertise ensures the production of high-quality PCBs, which are essential for the functionality and efficiency of electronic products.
What are the main types of PCB manufacturers?
PCB manufacturers can be categorized into domestic and international, as well as specialized and general manufacturers. Domestic manufacturers provide advantages like shorter lead times, while international ones may offer lower costs. Specialized manufacturers focus on niche markets, whereas general manufacturers serve a wider range of sectors.
What are the key processes in PCB manufacturing?
The key processes in PCB manufacturing include design, fabrication, and assembly. The design phase entails creating schematics, followed by fabrication techniques such as printing and etching. Assembly methods like Surface Mount Technology (SMT) and Through-Hole Technology (THT) connect components to the physical boards.
How is quality control maintained in PCB manufacturing?
Quality control in PCB manufacturing is ensured through adherence to stringent standards and certifications like IPC-A-600 and ISO 9001. Manufacturers utilize various testing methods, such as Automated Optical Inspection (AOI) and Functional Testing, to verify that every PCB meets performance and reliability requirements.
What are current trends in PCB manufacturing?
Current trends in PCB manufacturing include advances in automation, machine learning, and environmentally friendly practices. Innovations are enhancing production speed and capabilities, while the adoption of lead-free solder and closed-loop systems promotes sustainability and efficient use of resources in the industry.