Investing in a block making machine can be a game changer for businesses in the USA, especially in the construction and manufacturing sectors. With the right machine, companies can improve productivity and reduce costs, but several key factors must be considered before making this significant investment. This article explores essential considerations like market demand, technology advancements, and cost-effectiveness, helping businesses make informed decisions that align with their goals.
For businesses seeking reliable equipment, Lontto Block Making Machine offers innovative solutions designed to meet varying production needs, ensuring efficiency and quality in every block produced.
Market Demand Analysis
Market demand plays a crucial role in deciding whether to invest in a block making machine. Understanding the demand for construction materials in the local area helps businesses align their production capabilities with current needs.
Understanding Local Needs
Understanding local needs involves assessing the types of construction projects prevalent in the region. Research local construction trends, such as residential or commercial developments, that may impact the demand for blocks. Evaluate the specific materials favored in the area, including concrete or eco-friendly options. Engaging with local contractors and builders provides insights into their requirements and the market landscape. Identifying peak construction seasons also aids in planning production schedules effectively.
Assessing Competition
Assessing competition entails analyzing existing block manufacturers within the area. Identify the number of competitors and their market share to gauge the saturation level. Evaluate their pricing strategies, production quality, and customer service. This analysis helps businesses pinpoint gaps in the market, offering opportunities to differentiate their products. Establishing relationships with local suppliers can also create competitive advantages. Conducting a SWOT analysis (Strengths, Weaknesses, Opportunities, Threats) enables businesses to make informed decisions based on their findings related to competition.
Machine Specifications
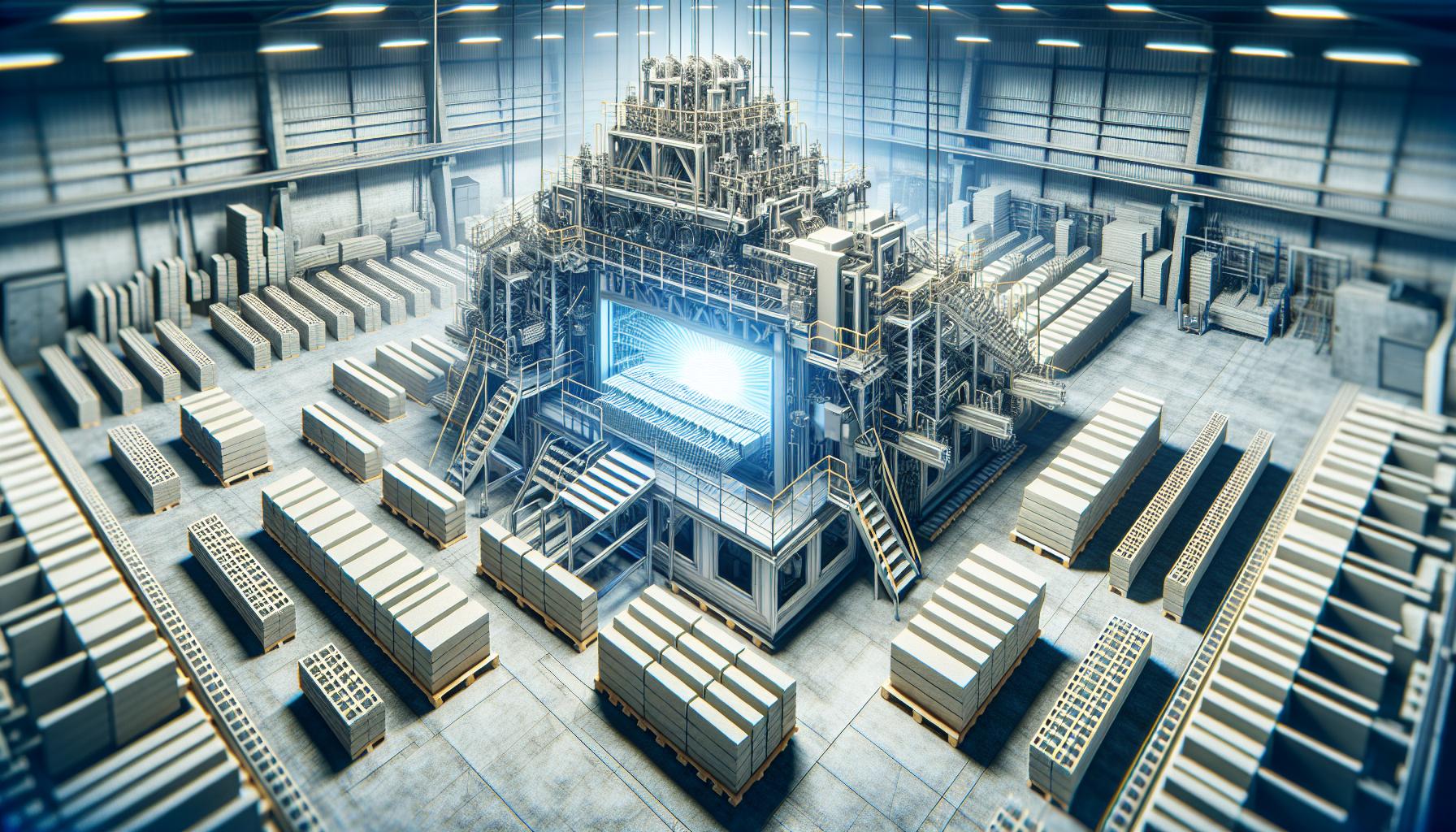
Investing in a block making machine necessitates a careful examination of its specifications. These specifications dictate the machine’s performance, suitability, and overall effectiveness in meeting a business’s production needs.
Types of Block Making Machines
- Manual Block Making Machines: These require manual labor for operation, making them cost-effective for small-scale producers. They typically produce fewer blocks per hour than automatic machines.
- Semi-Automatic Block Making Machines: These offer a balance between manual and fully automated operations, allowing for some level of automation while still requiring manual intervention for loading and unloading.
- Fully Automatic Block Making Machines: These machines operate independently with minimal human involvement. They provide high production rates, advanced technology, and automation, making them ideal for large-scale operations.
- Production Capacity: Determine the number of blocks produced per hour. This helps evaluate whether the machine meets business demands.
- Power Consumption: Analyze the machine’s energy requirements. Machines with lower power consumption reduce operational costs and increase profitability.
- Material Compatibility: Assess the types of materials the machine can use, such as concrete or clay. Compatibility impacts flexibility in product offerings.
- Size and Dimensions: Review the machine’s physical dimensions and weight. Ensure it fits in the available workspace and meets transportation requirements.
- Control System: Examine the machine’s control interface. Advanced control systems provide greater precision and efficiency in operations.
- Maintenance Requirements: Refer to the maintenance guidelines. Easy-to-maintain machines minimize downtime and extend lifespan.
- Warranty and Support: Verify warranty terms and customer support availability. Robust support options improve long-term satisfaction with the investment.
Financial Considerations
Investing in a block making machine requires thorough financial planning. Businesses in the USA must analyze both initial costs and ongoing expenses to ensure profitability.
Initial Investment Costs
Initial investment costs encompass the purchase price of the block making machine, installation fees, and any necessary accessories. Businesses should evaluate different machine types—manual, semi-automatic, and fully automatic—to ascertain the most suitable option for their production needs. Prices for these machines typically range between $5,000 and $100,000, depending on the specifications and technology. Additionally, consider costs related to site preparation, equipment transportation, and any workforce training required to operate the machine.
Operating Expenses
Operating expenses fluctuate based on the machine’s specifications and production volume. Key factors include energy consumption, maintenance, raw material costs, and labor. For example, higher energy-efficient machines may reduce electricity costs, while regular maintenance can prevent significant breakdowns and extend the machine’s lifespan. Businesses should budget for raw materials like cement, sand, and aggregates, which may vary in price depending on local market trends. Assessing these operating expenses helps ensure long-term financial stability and boosts overall profitability.
Supplier Evaluation
Supplier evaluation plays a crucial role in selecting the right block making machine for businesses in the USA. Companies must assess several key factors that contribute to a supplier’s capabilities.
Reputation and Reliability
Reputation and reliability of a supplier significantly impact the investment’s success. Companies should research suppliers’ market presence, customer reviews, and track records. A strong reputation often indicates consistent quality and trustworthy service. Successful suppliers maintain transparency about their machines’ performance and address customer concerns promptly. Businesses can verify credibility through industry certifications and references from established customers.
After-Sales Support
After-sales support is essential for maximizing machine performance and longevity. Businesses must evaluate the level of support a supplier provides post-purchase. This includes availability of technical assistance, warranty coverage, and parts replacement services. Reliable suppliers offer comprehensive training for machine operators and ongoing maintenance advice. Understanding the terms of warranty and support ensures businesses can address issues quickly, minimizing downtime and maintaining productivity.
Regulatory Compliance
Businesses in the USA must navigate a landscape of regulations when investing in a block making machine. Compliance with local, state, and federal regulations ensures safe and efficient operations while avoiding legal issues.
Understanding Local Regulations
Local regulations often dictate manufacturing standards, safety protocols, and zoning requirements. Businesses must research specific regulations relevant to their operating area. Consulting local authorities or legal advisors can provide essential guidance on compliance, ensuring that the investment aligns with community standards and legal expectations.
Environmental Considerations
Environmental regulations play a significant role in the manufacturing sector. Businesses must consider waste management, emissions control, and resource consumption when selecting a block making machine. Obtaining the necessary permits and ensuring compliance with the Environmental Protection Agency (EPA) guidelines is crucial. Sustainable practices not only meet legal requirements but can also improve a company’s reputation and appeal to eco-conscious consumers.
Conclusion
Investing in a block making machine can significantly benefit businesses in the USA’s construction and manufacturing sectors. By carefully considering market demand technological advancements and financial implications companies can make strategic choices that align with their goals.
Understanding local construction trends and engaging with contractors offers valuable insights that can shape production strategies. Additionally evaluating machine specifications and supplier reliability ensures that the investment supports long-term operational efficiency.
Lastly managing regulatory requirements and implementing sustainable practices not only fosters compliance but also enhances a company’s reputation. With thoughtful planning and analysis businesses can maximize the potential of their block making machine investment.
Frequently Asked Questions
What are the benefits of investing in a block making machine?
Investing in a block making machine can greatly enhance productivity and reduce costs for businesses in the construction and manufacturing sectors. It enables faster production, lower labor costs, and the ability to meet specific market demands effectively.
How can I assess market demand for block making?
Conducting market demand analysis is key. Understand local construction trends by engaging with contractors, researching current projects, and identifying preferred materials in your region. This insight helps tailor your production to meet local needs.
What types of block making machines are available?
Block making machines come in three main types: manual, semi-automatic, and fully automatic. Each serves different production scales and needs, so it’s important to evaluate production capacity and operational requirements when making a choice.
What financial considerations are important for this investment?
Review initial costs, ongoing operating expenses, and potential returns. Initial costs range from $5,000 to $100,000, depending on machine specifications. Evaluate energy consumption, raw materials, and maintenance to ensure profitable long-term investments.
How should I evaluate suppliers for block making machines?
When evaluating suppliers, consider their reputation, quality of service, customer reviews, and market presence. Reliable suppliers should offer strong after-sales support, including training, warranty coverage, and maintenance advice to ensure optimal machine performance.
What regulatory compliance should I be aware of?
Businesses must comply with local, state, and federal regulations related to manufacturing standards, safety protocols, and environmental guidelines. Consulting legal advisors and local authorities can help navigate these requirements effectively.
Why is environmental compliance important for block making?
Adhering to environmental regulations not only ensures compliance but enhances your business reputation. Sustainable practices attract eco-conscious consumers and can lead to cost savings through efficient resource use and waste management.